When you need stainless steel fabricators for your project, you need a team of professionals with ample skill and know-how. You need an organization dedicated to working closely with you to achieve your best results. Take into consideration what the company can do for...
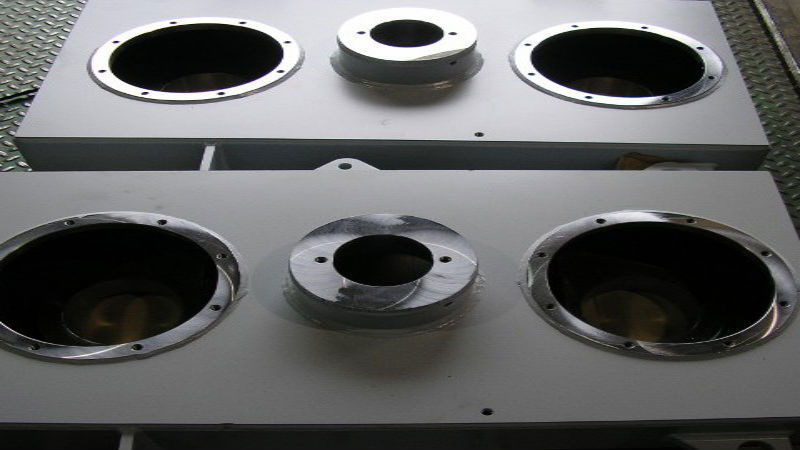