When it comes to custom aluminum shapes, the extrusion process is one of the best options. It allows for the entire shape to be created from one seamless piece of aluminum, which limits fabrication and the need for welding or joining. With original aluminum extrusion...
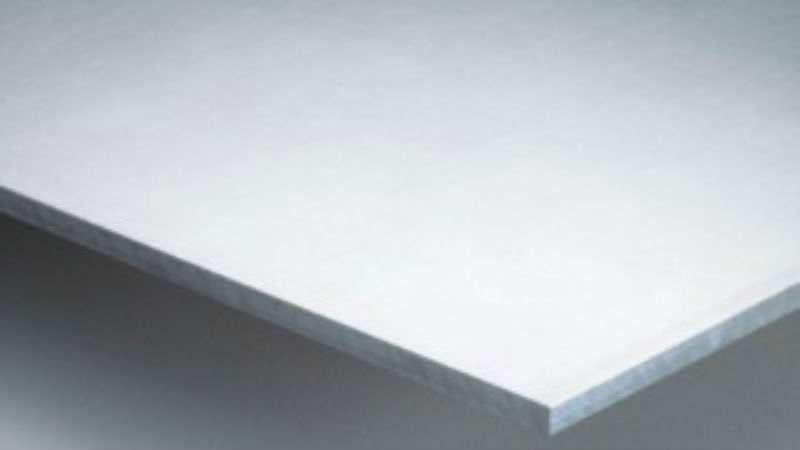